 |
|
Eyetronics reveal to MI6 how they turned the ice
dragsters and helicopters from models to digital
objects for the "Die Another Day" computer
animators and special effects wizards...
|
|
Eyetronics Interview - Digitizing Bond's Vehicles
25th August 2003
When vehicles needed to be moved from physical models
into digital cyberspace during "Die Another Day" production,
Eon Productions turned to specialist 3D acquisition company
Eyetronics.
The company, which is based in Belgium and California,
specializes in high-quality 3D acquisition systems that
enabled faster production of 3D models, so that the 007
animators and special effects wizards could get their hands
on Bond's toys faster than ever before. |
|
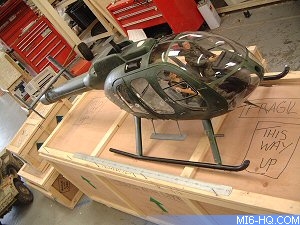
Above: A scale model of the Hughes
NOTAR from the climatic finale of "Die Another Day" |
With deadlines extremely tight on the project, Eyetronics were
called in to use its unique ShapeWare system to digitally capture
and model Gustav Graves` ice dragster and the Hughes NOTAR helicopter
for scenes in which they could not be filmed for real.
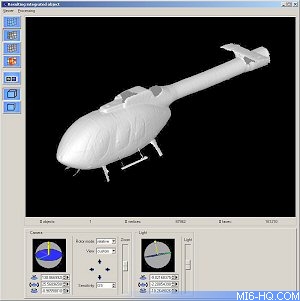
Above: The specialist ShapeSnatcher software |
|
Scanning on Location
For "Die Another Day", Eyetronics staff went
on location to Pinewood Studios in London to scan scale
models of the vehicles from all angles. The scans were
taken back to Eyetronics’ offices, where they were
processed and assembled in 3D using ShapeSnatcher software.
The ShapeWare process starts with ShapeCam, a hand-held
scanning system that consists of a digital camera and a
specially designed flash device mounted on a lightweight
frame. It allows users to freely move around persons or
objects, capturing dimensional and texture information
by simply taking pictures. ShapeCam can capture objects
ranging from about four inches to eight feet in height.
A face or head can be captured in about 10 minutes and
a full body in approximately 15 to 30 minutes. |
Completed 3D models of the dragster and helicopter were output
as .obj files and sent to Cinesite and Double Negative post-production
houses in London, where they were rendered with Maya software
and composited into the appropriate scenes. The model production
took just two weeks.
“
Normally we would ask a post-production house to do all the modeling
and texturing,” says Sharon Lark, visual effects producer
for the film. “It was much more time- and cost-efficient
to use Eyetronics’ services. Eyetronics allowed us to dedicate
our resources to finishing other work, rather than spending weeks
building and texturing the model as we would normally have to
do.”
Peter Bebb, a 3D artist with Double Negative, says the Eyetronics
scans sped up post-processing of the final 3D helicopter model. “Data
derived from the scan allowed us to build and texture the final
computer graphic element with good results in a relatively short
time frame.”
Realism Without Filming
The final product looks as if the actual vehicles were
used, Lark says.
“ Eyetronics provides a fully 3D object that looks photorealistic,” she
says.
“We were able to put the 3D helicopter model into scenes in which
it would have been impossible to use a real helicopter for safety reasons.”
The portability of the ShapeWare system allowed MGM Europe
to supervise the scanning session without leaving the filming
site, which is a valuable asset to studios with a constant
eye on the bottom line.
Right: Before and after - the ice dragster recreated digitally. |
|
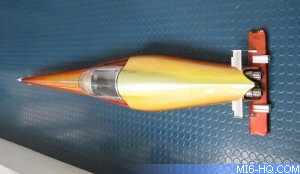
Above: A scale model of the ice dragster
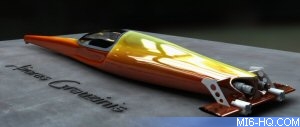
Above: A 3D render
of the scanned data model.
|
“The ShapeWare system allows us to come to the client’s
site, which translates into significant time and money savings,” says
Dirk Callaerts, Eyetronics’ CEO. “In this case, it
would have been expensive to ship the scale models from London.
In other cases, we need to do scans of actors and actresses whose
time is too valuable to be away from the set during filming.”
Thanks
to Eyetronics for their assistance. All images © copyright
Eyetronics 2002, used with permission.
Related Articles:
Digital
Illusions - The Computer Effects Used In "Die Another Day"